360 Degree Syrup Cap Inspection Using DeepInspect
360 Degree Syrup Cap Inspection Using DeepInspect
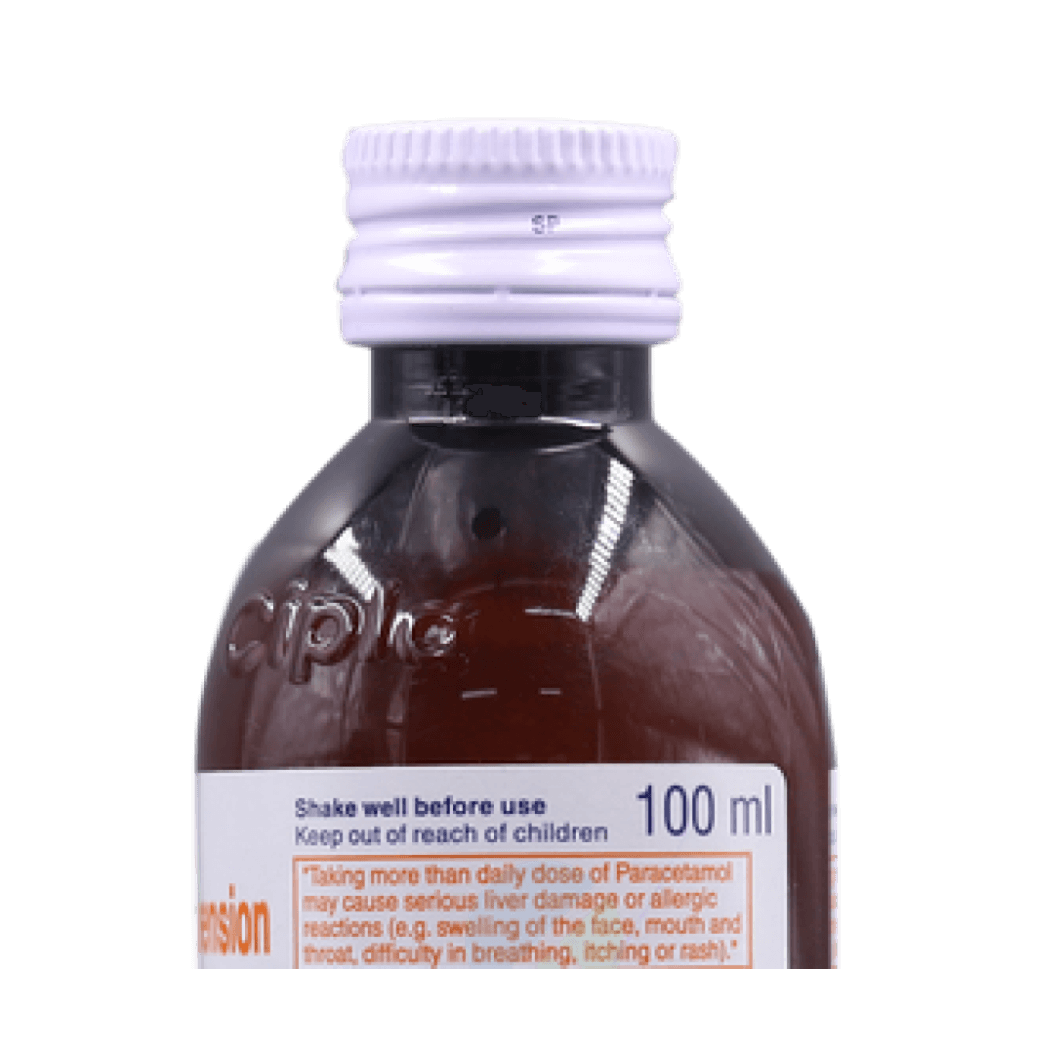
Related Articles
Introduction
Quality control in packaging can make or break product integrity, especially for sensitive products like pharmaceutical syrups. Even minor flaws—such as dents, missing seals, or improperly threaded caps—can lead to leakage, contamination, and ultimately a loss of consumer trust. For pharma companies, these defects pose not only a threat to product safety but also to regulatory compliance and brand reputation.
Common Syrup Cap Defects in Pharma and Their Impact on Product Quality and Compliance
Here’s an overview of common defects on syrup caps and their potential outcomes:
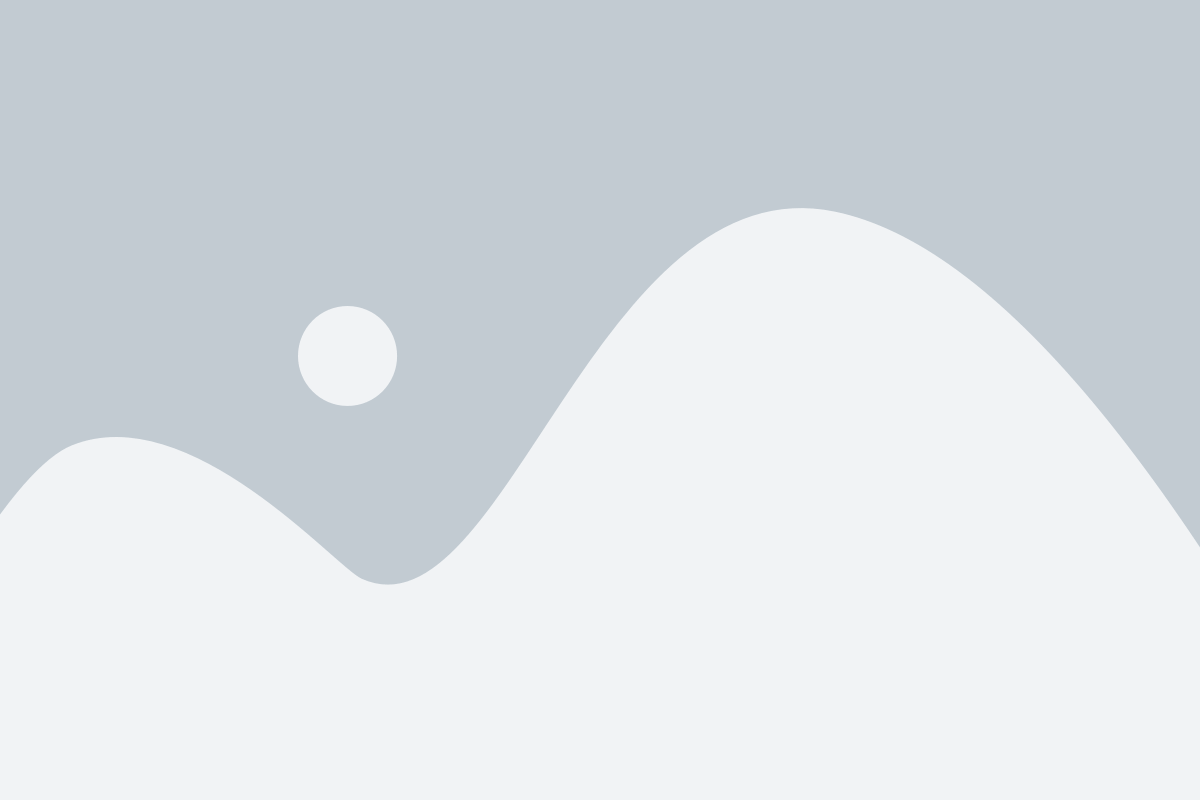
Dents and Cuts:
Physical deformities such as dents or cuts on caps can compromise the cap’s seal, allowing air, contaminants, or bacteria to enter the bottle. This can lead to contamination risks, impacting the quality and safety of the syrup. Over time, this could result in product spoilage, posing health risks to consumers.
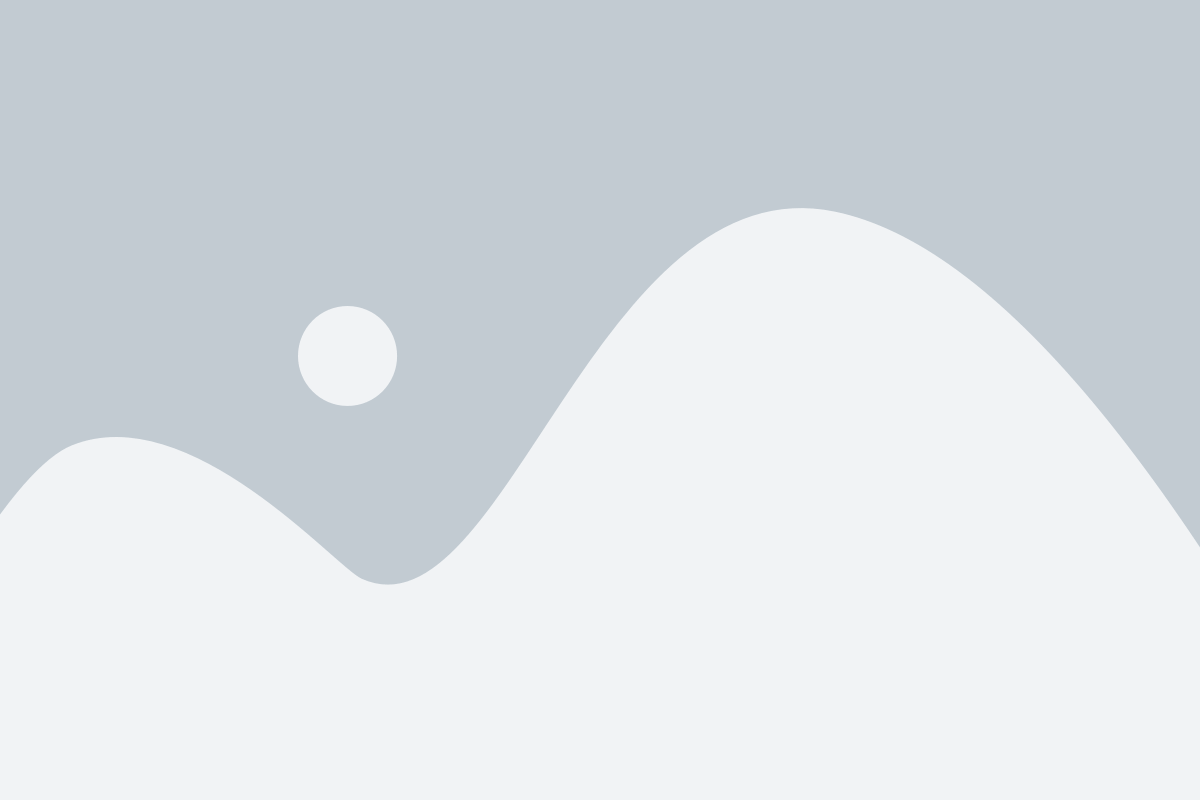
Missing or Improper Seals
Seals are critical for maintaining sterility and preventing leaks. Missing or improperly applied seals can lead to leakage, which affects not only product integrity but also can create messy handling issues for consumers. Furthermore, an unsealed product is exposed to environmental contaminants, leading to a shorter shelf life and a higher likelihood of consumer complaints.
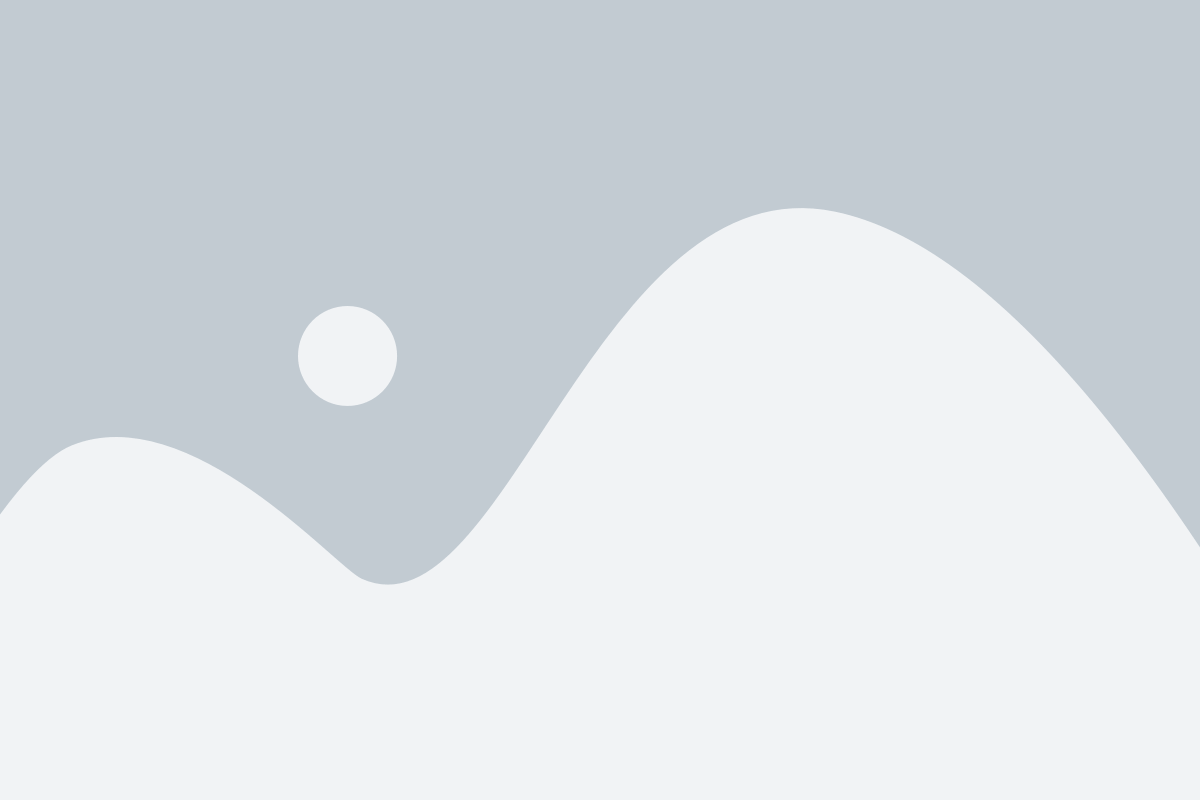
Missing Threads
Caps rely on threading to fit securely onto the bottle neck. If threads are missing or damaged, the cap may not fit tightly, leading to leaks or loose closures. This can result in product wastage and contamination risks, diminishing product reliability and potentially affecting the brand's reputation.
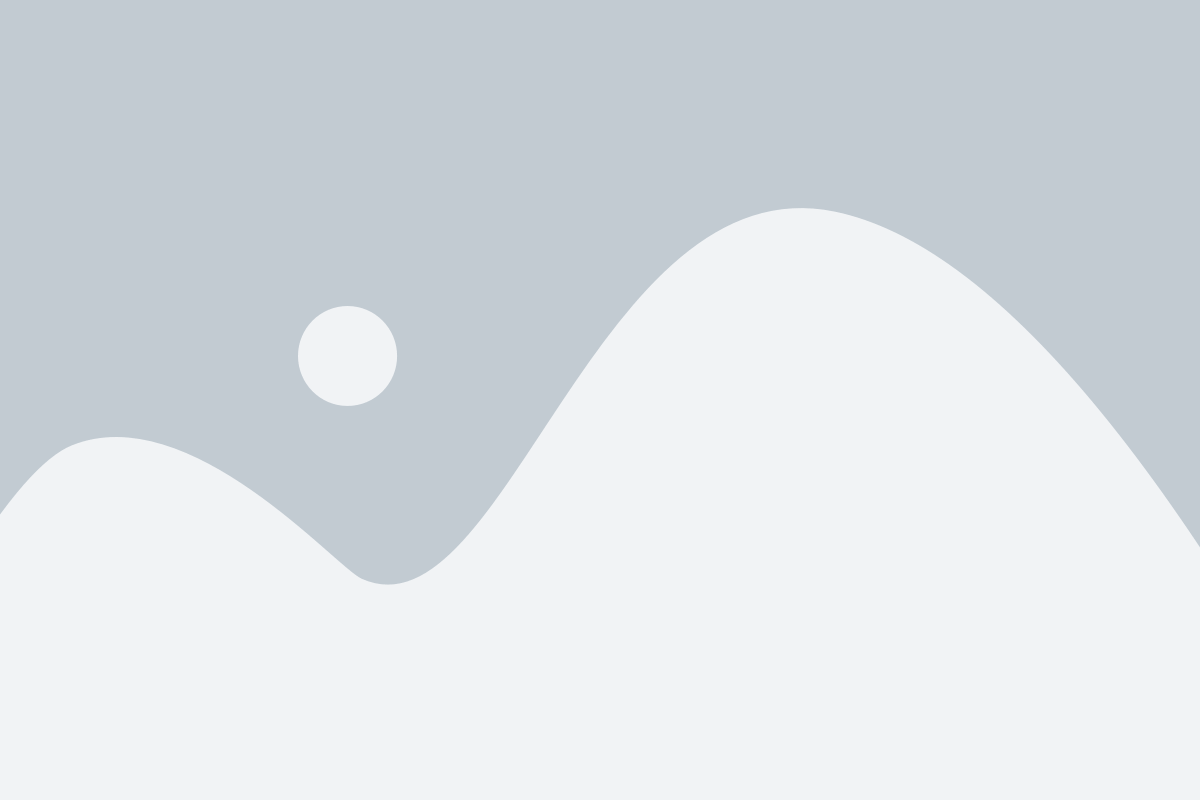
Improper Torque Application
During the capping process, incorrect torque (too much or too little) can cause the cap to either be too loose or too tight. A loose cap may lead to leakage or contamination, while an overly tight cap might cause the consumer difficulty in opening it or even damage the bottle.
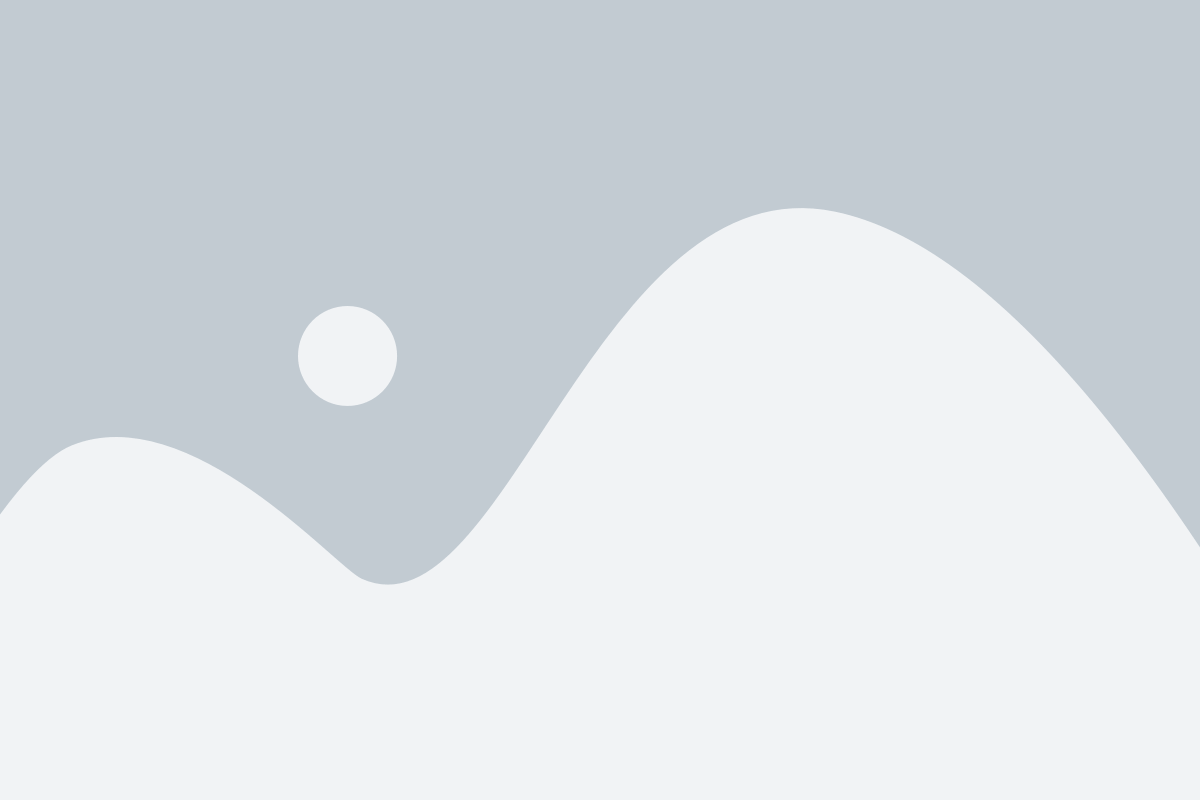
Improper Torque Application
During the capping process, incorrect torque (too much or too little) can cause the cap to either be too loose or too tight. A loose cap may lead to leakage or contamination, while an overly tight cap might cause the consumer difficulty in opening it or even damage the bottle.
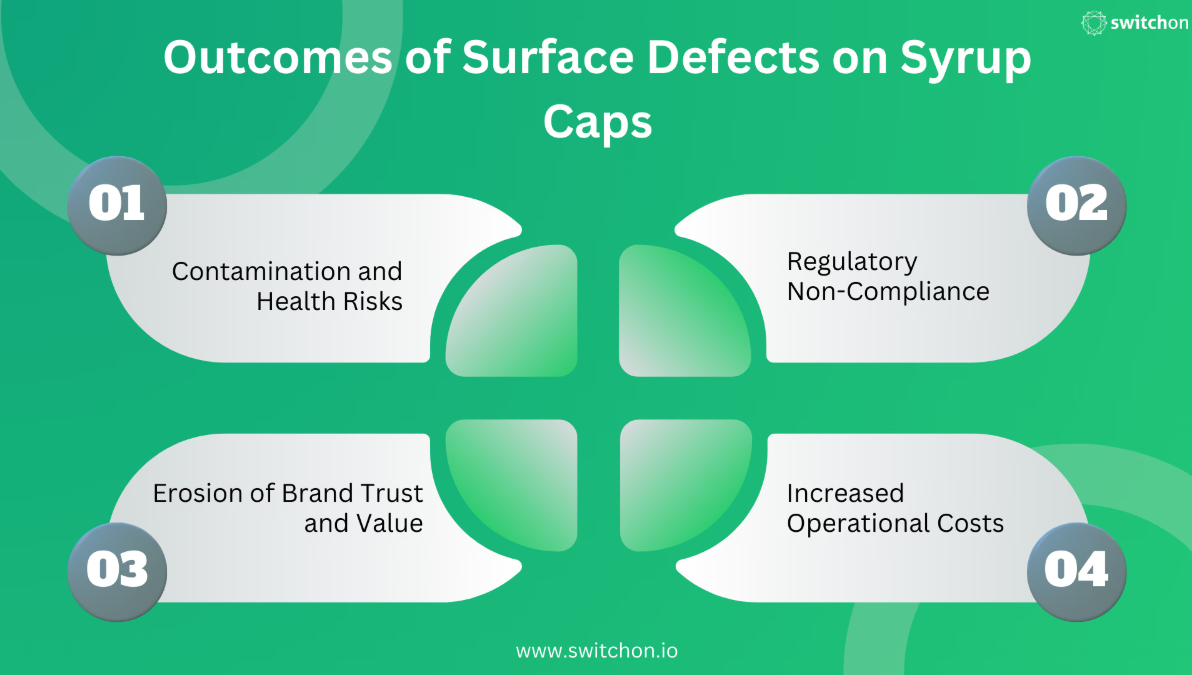
DeepInspect® - FDA CFR Complaint Software for Pharma Quality Inspection
DeepInspect® is an FDA CFR-compliant, AI-powered visual inspection software designed specifically for syrup cap quality control in the pharmaceutical industry. It identifies surface defects on syrup caps with remarkable 99.5% accuracy, even on high-speed production lines. By detecting issues like dents, missing seals, and improper threading, DeepInspect® ensures that only defect-free products reaches the market, helping manufacturers maintain compliance, protect consumer safety, and uphold brand reputation.
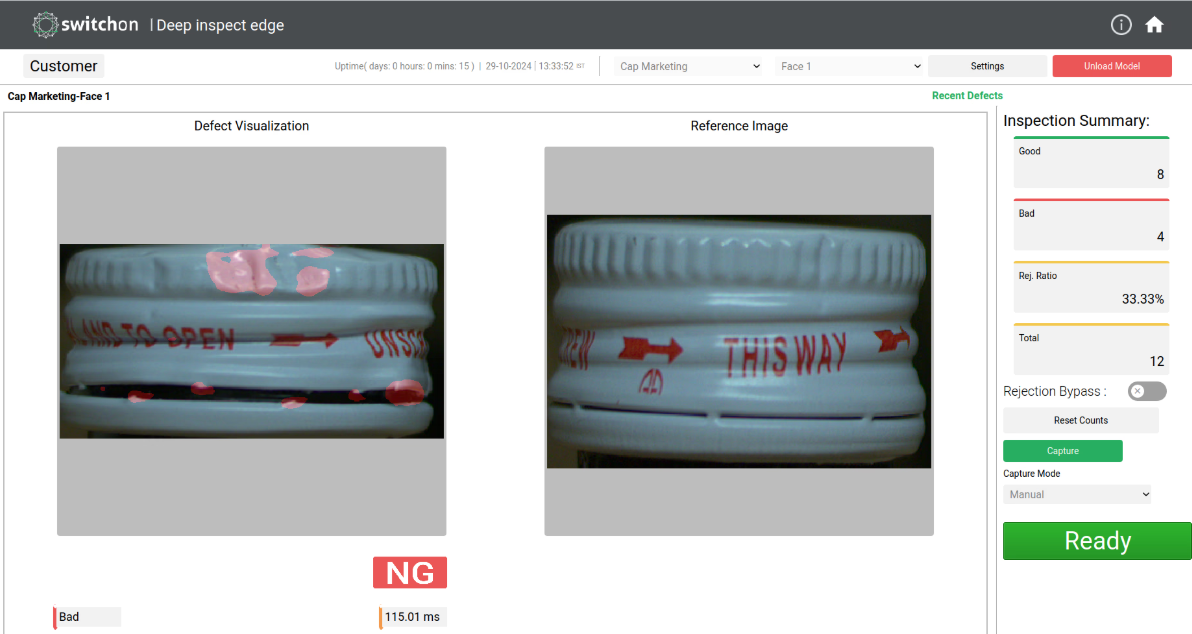
Key Components of the DeepInspect® Setup
DeepInspect Software: The AI-powered system at the heart of inspection.
Industrial Controller: Equipped with an i5 processor and GPU for fast data processing.
Industrial Vision Lights & Camera: Ensure high-quality images for precise defect detection.
Mitsubishi PLC: Controls conveyor speed and system coordination for seamless operation.
How DeepInspect® AI- Powered Syrup Cap Inspection works?
After filling, each bottle is transferred to the capping machine on a conveyor belt, aligned in a single file to position each bottle precisely under the capping head. As a bottle arrives at the capping head, a cap is placed on its mouth, and a spindle or chuck capper twists and fastens it securely.
The capped bottle then moves to the SwitchOn DeepInspect® station, where two side cameras and one top camera provide a 360-degree inspection to detect defects such as cuts, missing seals, and dents—with 99.5% accuracy. Strategically positioned lighting enhances visibility, ensuring each camera captures clear, detailed images for a thorough inspection, so only bottles with flawless caps continue forward.
Why Choose DeepInspect® for Visual Quality Inspection in Pharma
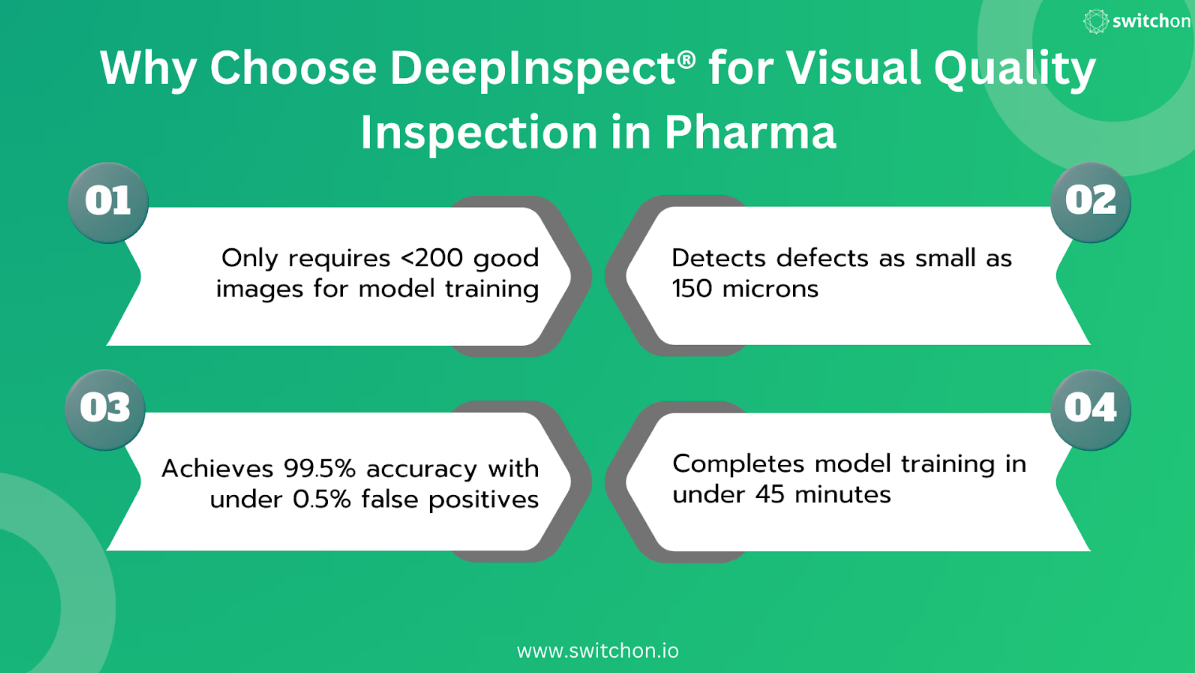
Conclusion:
DeepInspect® offers a powerful solution for syrup cap inspection, detecting even the smallest surface defects with precision to ensure product quality. By optimizing production efficiency and reducing the need for manual labor, it streamlines operations while lowering costs. DeepInspect® consistently delivers defect-free products that meet the strictest quality standards, reinforcing brand reputation and trust in the process.
Let's Discuss How We Can Transform Your Operations!
FAQ’s :
DeepInspect uses readily available industrial-grade hardware to ensure high repeatability and long lifespan. We provide a basic kit to help you get started, which includes a controller, camera, lights, and a PLC.
DeepInspect supports inspection speeds of up to 1000 parts per minute. The final speed depends on various factors, such as the number of cameras, lighting, and other line conditions. If you have a requirement above 1000 PPM, please contact us.
We support Area Scan, Line Scan, and Thermal cameras. Our software is compatible with industry-standard vendors like Basler, Baumer, Allied Vision, FLIR, and others.
DeepInspect has successfully inspected over 1000 unique SKUs across automotive, pharma, electronics, and FMCG industries. Check out our [case studies](#) to learn more.
Curious to Learn More?
Download the full use case below!