Glass Bottle Bore Inspection Using DeepInspect®
Revolutionizing Glass Bottle Quality Control: The Power of AI-Powered Bore Inspection
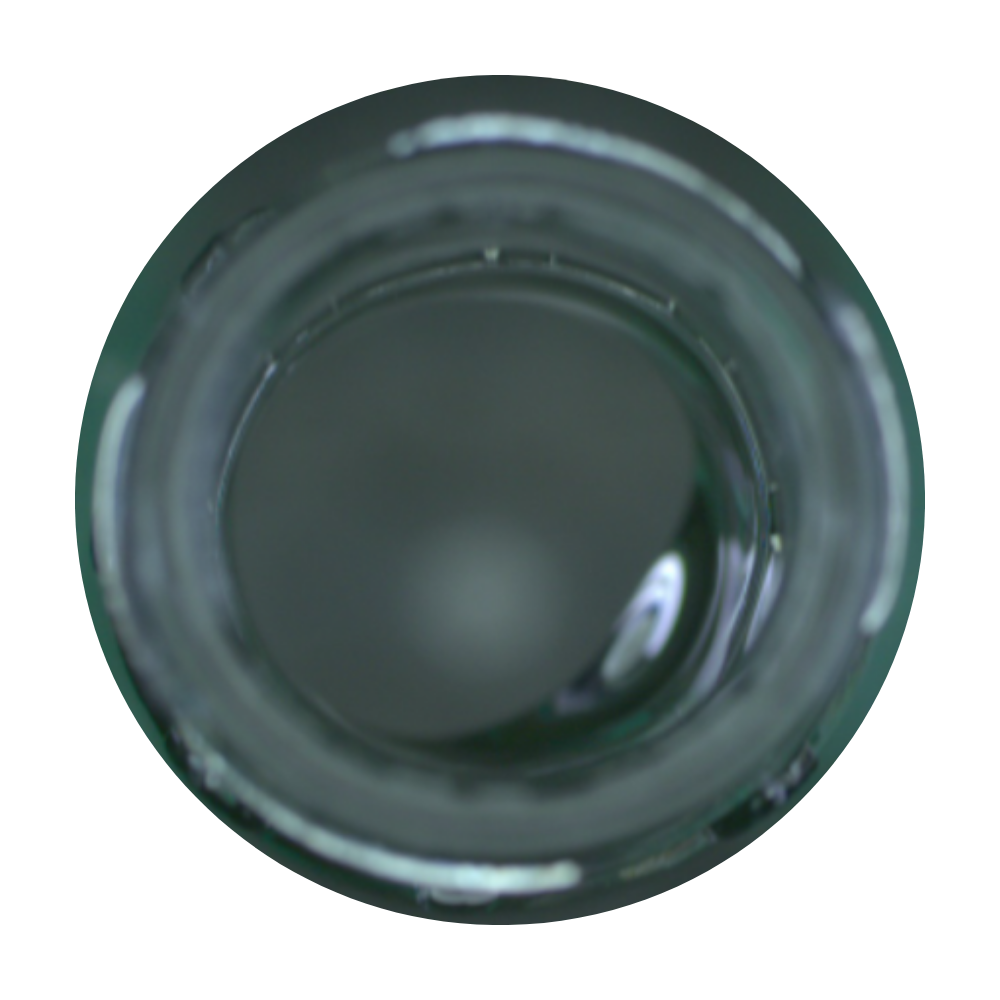
Related Articles
Introduction
In today’s fast-paced FMCG landscape, product quality and consistency are non-negotiable. Glass bottles, a staple packaging choice for beverages, pharmaceuticals, and food products, must meet stringent quality standards. Even minor defects in glass containers can disrupt production, trigger consumer complaints, and tarnish brand reputation. This is where advanced AI-driven inspection software- DeepInspect® is transforming traditional quality control methods, ensuring precision and efficiency in glass bottle production.
Why Glass Bottles are Widely Used in the FMCG Industry
Glass bottles continue to dominate packaging in the FMCG sector for several reasons.Given these advantages, maintaining flawless glass containers is crucial for brands aiming to deliver exceptional customer experiences.
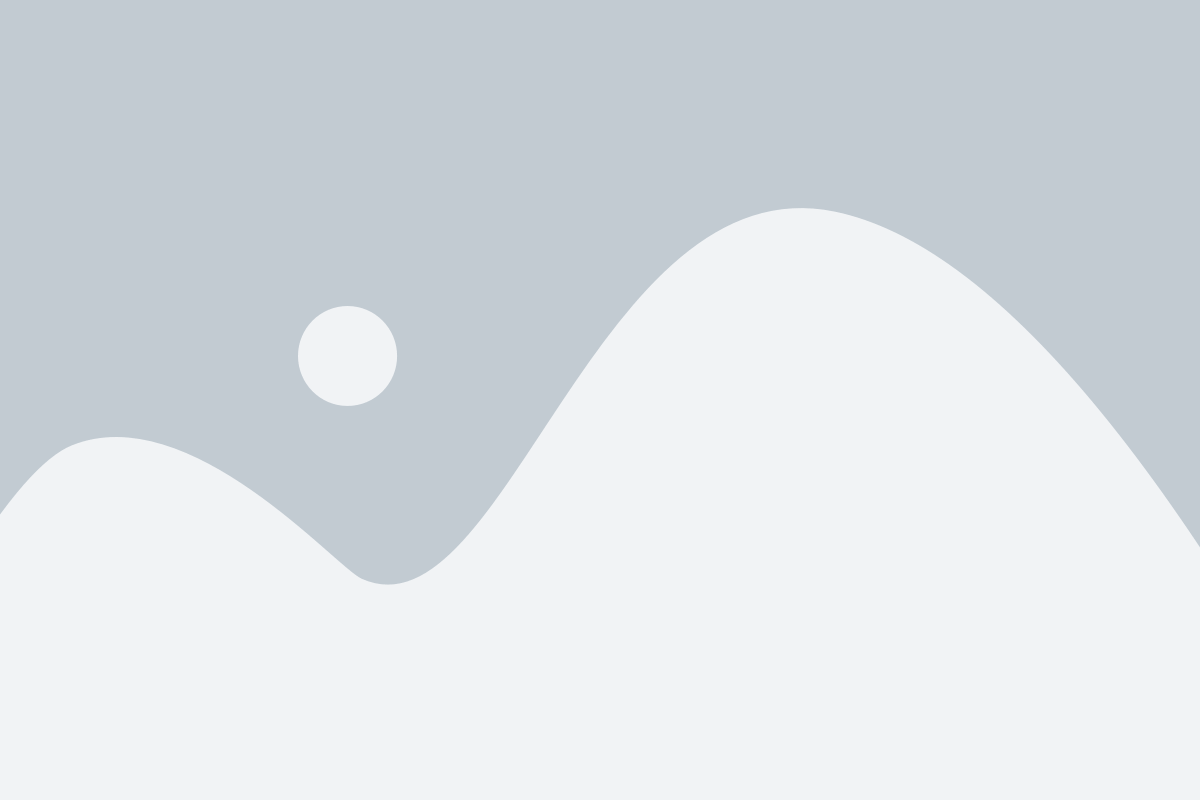
Superior Barrier Properties
Glass is completely impermeable, effectively preserving the product's original taste, and overall quality
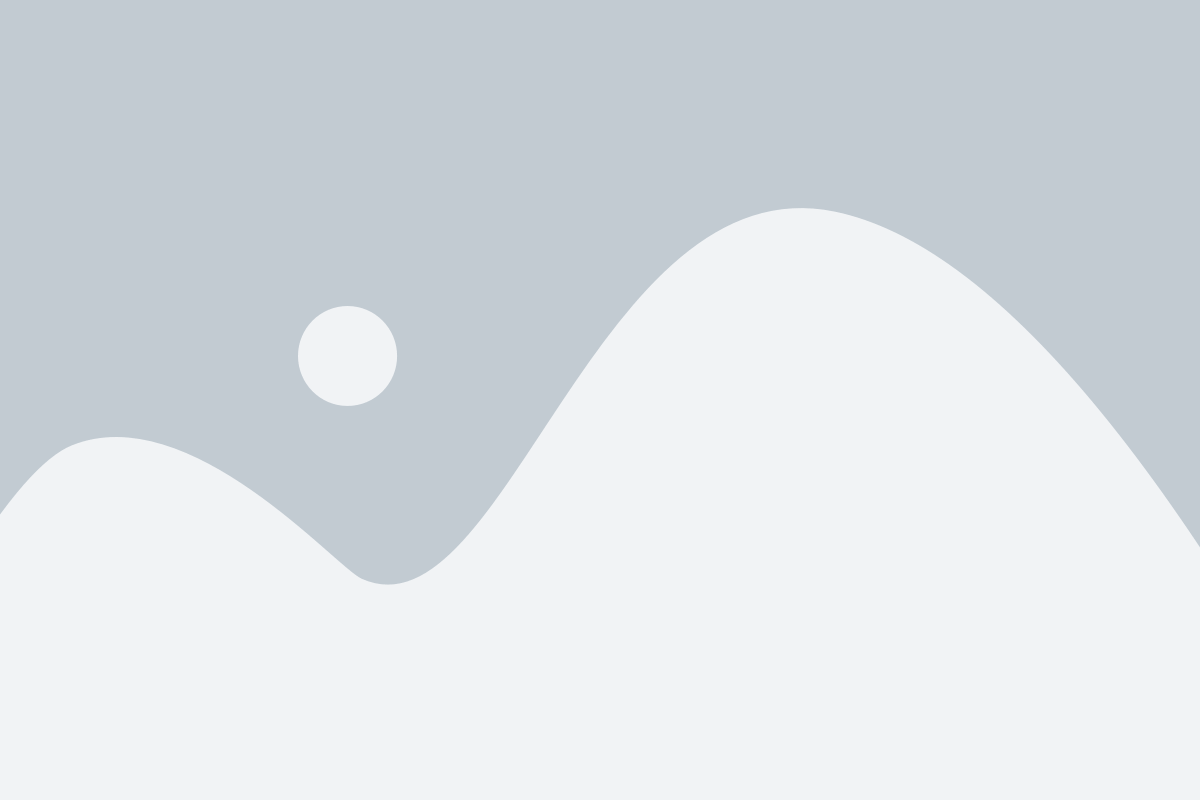
Recyclability
Glass is 100% recyclable without any loss of quality, actively supporting eco-friendly and sustainable practices worldwide
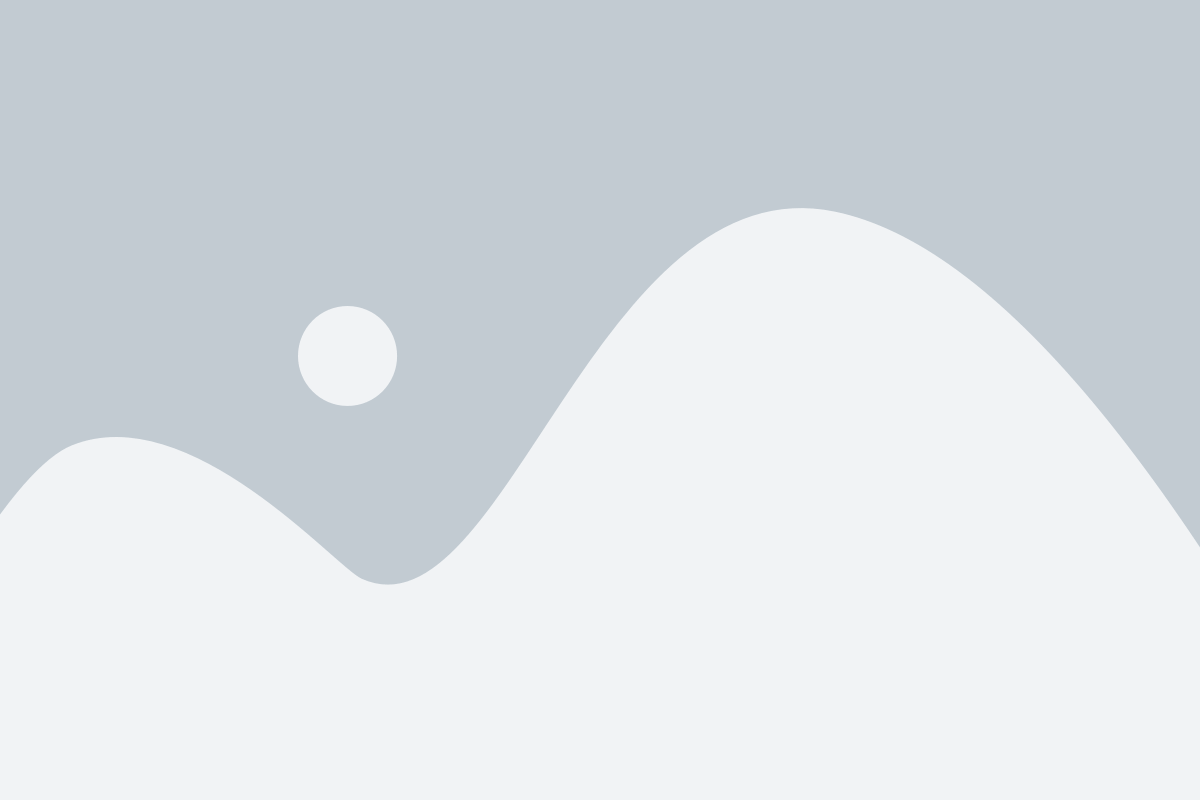
Premium Appeal
Glass packaging significantly enhances product aesthetics, elegantly conveying a strong sense of premium quality, sophistication, and luxury
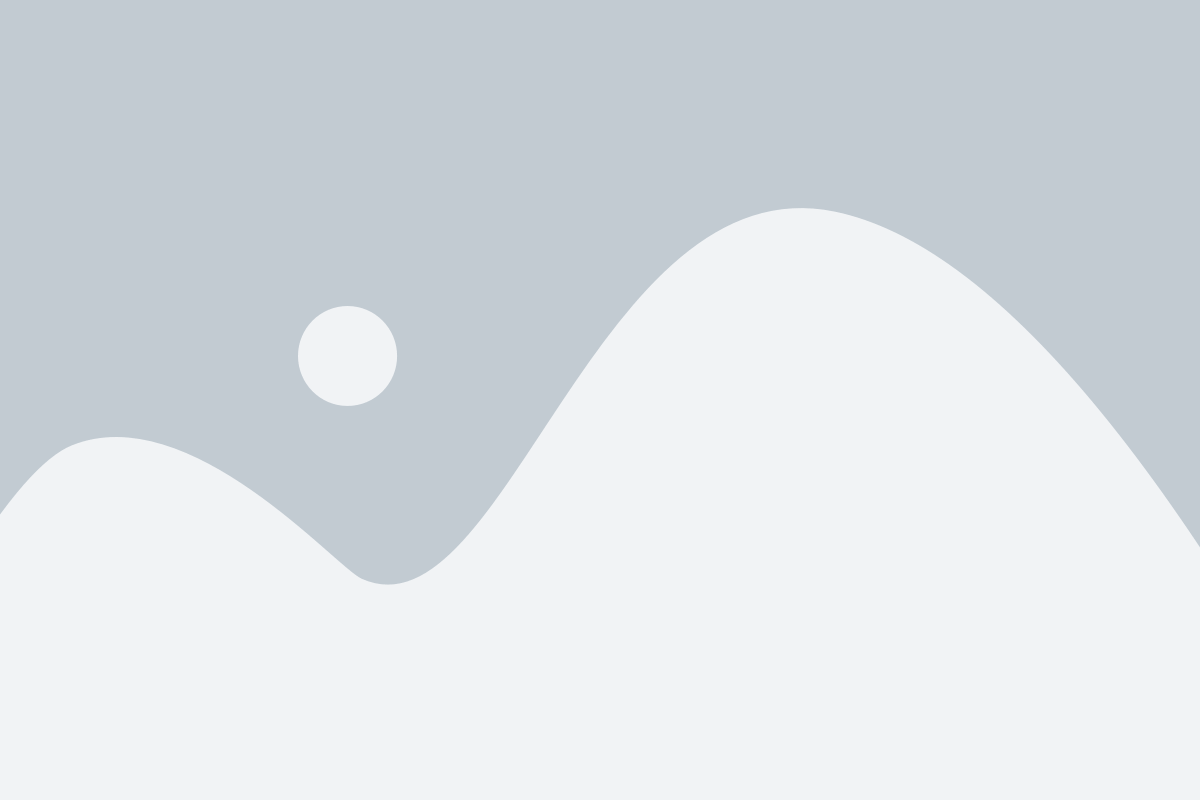
Chemical Inertness
Unlike plastics, glass does not react with its contents, making it ideal for F&B and Pharmaceutical
Types of Defects in Glass Bottle Bores & What Causes these Defects?
The bore of glass bottles is highly prone to defect formation. The bore, or neck region, of a glass bottle is critical for functionality. —ensuring proper sealing, filling, and user experience. However, defects in this area are common due to various factors in the manufacturing process.
1. Molten Glass Distribution Variations
During the blow moulding process, molten glass is shaped into bottles. Inconsistent distribution of molten glass can result in defects like choked, bent, or hollow necks. Factors such as uneven temperature control, improper mould alignment, or fluctuations in glass viscosity often contribute to these variations, leading to critical quality issues in the bore region.
2. Equipment Wear and Misalignment
Over time, machinery used in glass bottle production, including moulds, conveyors, and blowers, undergo wear and tear. Misalignment of these components can cause deviations in bottle dimensions, particularly around the neck area. Regular maintenance is crucial, but even slight misalignments can lead to persistent defects if not promptly corrected.
3. Environmental Contaminants
Glass production environments are prone to dust, debris, and foreign particles that can infiltrate the manufacturing line. These contaminants can adhere to the bottle’s neck or get embedded during the forming process, compromising product quality. Effective air filtration, cleanroom protocols, and automated inspection are essential to mitigate this risk.
4. Human Error in Manual Processes
Manual inspection and handling remain common in many facilities, especially for niche or small-batch production. However, human error, fatigue, and inconsistencies in visual checks often result in missed defects or inaccurate assessments of bore quality. As production speeds increase, the likelihood of errors rises, making manual processes less reliable for critical inspections.
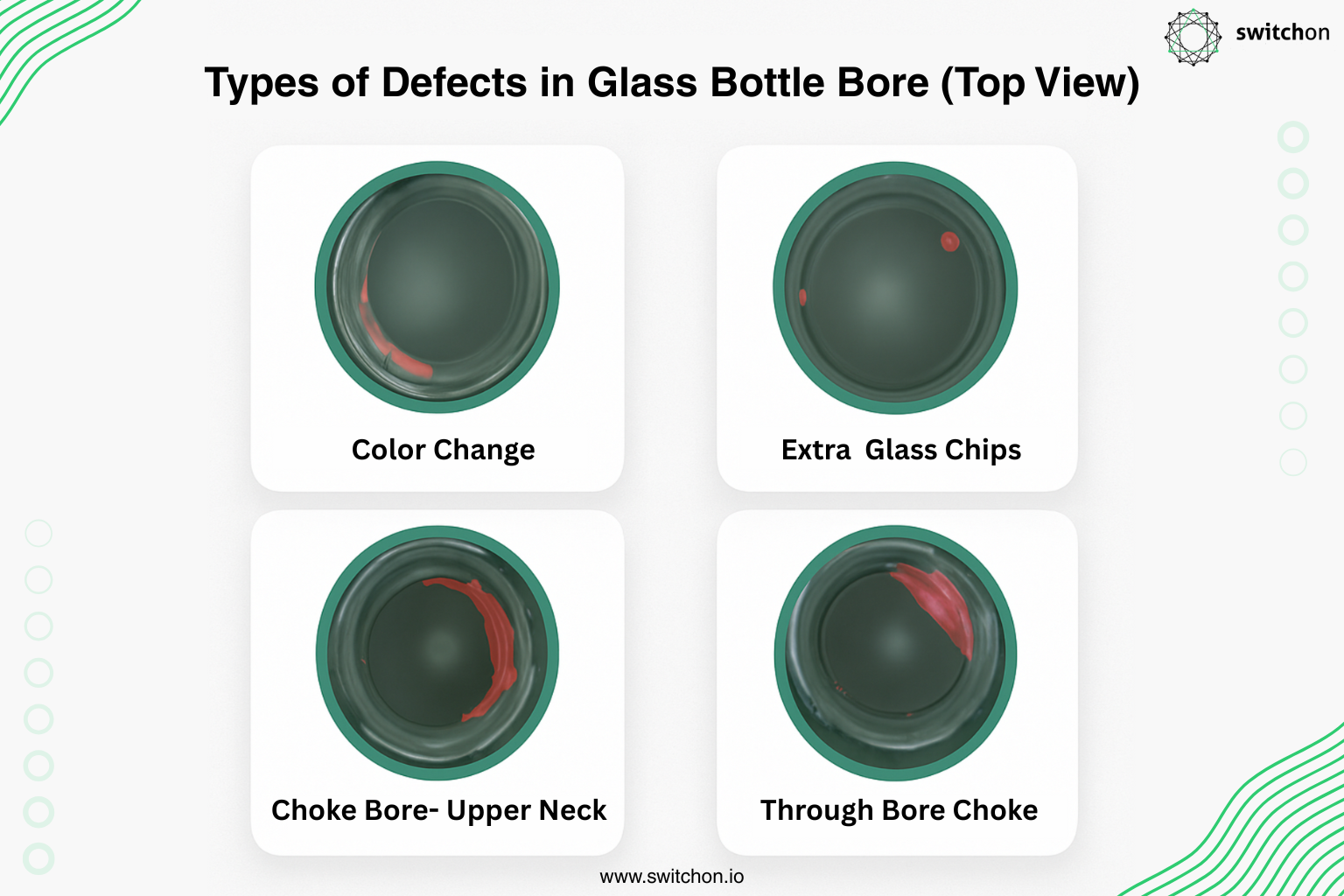
Why Traditional AI Systems Fail in Detecting Glass Bore Defects
While AI has been a buzzword in manufacturing, not all AI systems are created equal—especially when it comes to inspecting transparent, reflective materials like glass. Traditional AI inspection systems and manual methods face significant limitations:
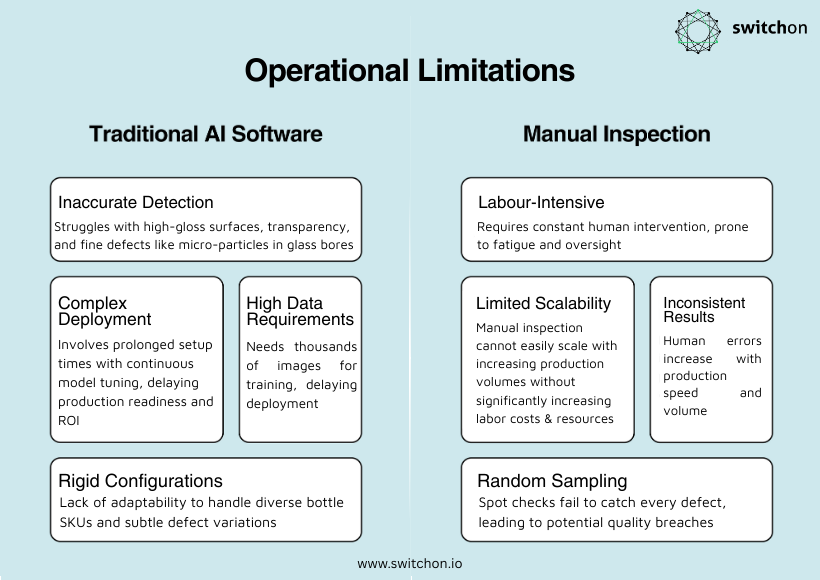
DeepInspect® - AI-Powered Quality Inspection Software for Glass Bottle Inspection
DeepInspect® is an AI-powered visual quality inspection software for glass bottle manufacturers that detects bore defects with high precision. It detects defects like choked necks (excess glass obstructing the bottle’s bore) and bent necks (misaligned bottle necks), etc. along with bore diameter inconsistencies and internal foreign particles. DeepInspect’s advanced machine vision with multi-angle cameras and AI algorithms analyze each bottle in real time, flagging even subtle deviations.
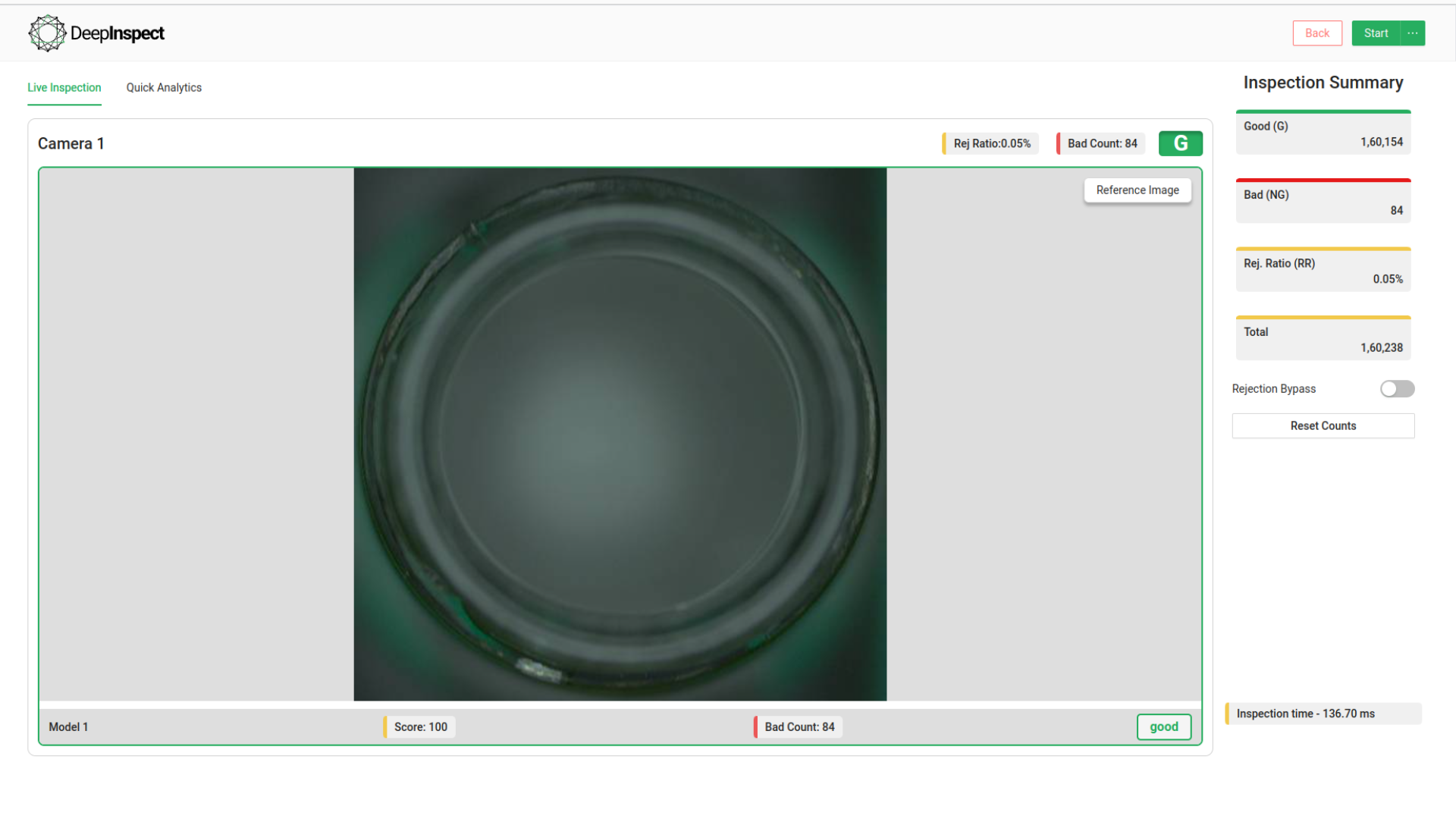
DeepInspect’s key advantages include 99.5% defect detection accuracy and minimal training data requirements. Unlike traditional vision systems, it learns from only a small set of good images, say just 200 nos, eliminating the need for thousands of defect samples. This high-precision, automated inspection runs at hundreds of bottles per minute, removing human error and ensuring faulty bottles are rejected immediately. By enabling reliable, rapid detection, DeepInspect® helps glass bottle manufacturers achieve zero-defect production lines, leading to improved product quality, safety, and efficiency.
Why Should Glass Bottle Manufacturers Choose DeepInspect® Over Traditional AI Inspection Systems?
Glass bottle manufacturers stand to gain immensely from adopting DeepInspect® due to its tailored approach and proven performance. DeepInspect® ensures 99.8% defect detection accuracy with minimal false positives of just 0.14%. It requires only 200 images for AI model training, enabling quick deployment without disrupting existing operations. The system performs comprehensive bore inspection—detecting choked necks, bent necks, hollow sections, small diameters, and foreign particles with high precision. With seamless inspection for multiple SKUs, DeepInspect® maintains consistent detection accuracy across diverse bottle variants. Real-time analytics and downloadable reports provide actionable insights for process optimization. By eliminating manual inspection, it help reduce labor costs, boosts operational efficiency, and delivers reliable, scalable quality control.
Impact of DeepInspect® in Glass Bottle Bore Inspection
The adoption of DeepInspect® can deliver transformative results for glass manufacturers:
- Zero Downstream Complaints: Enhanced defect detection ensures only flawless bottles reach customers.
- Improved Customer Satisfaction: Consistent quality builds trust with end clients.
- Increased Throughput: Automation accelerates inspection processes, keeping up with high production speeds
- Cost Savings: Reduction in manual labor and defect-related rejections translates to significant financial benefits.
Conclusion
In an industry where quality cannot be compromised, DeepInspect® stands out as a game-changer. Its AI-powered inspection capabilities provide glass bottle manufacturers with the precision, efficiency, and reliability they need to stay competitive in the FMCG market. By overcoming the limitations of manual and traditional AI systems, DeepInspect® ensures every bottle meets the highest quality standards—seamlessly, accurately, and efficiently.
Let's Discuss How We Can Transform Your Operations!
FAQ’s :
DeepInspect uses readily available industrial-grade hardware to ensure high repeatability and long lifespan. We provide a basic kit to help you get started, which includes a controller, camera, lights, and a PLC.
DeepInspect supports inspection speeds of up to 1000 parts per minute. The final speed depends on various factors, such as the number of cameras, lighting, and other line conditions. If you have a requirement above 1000 PPM, please contact us.
We support Area Scan, Line Scan, and Thermal cameras. Our software is compatible with industry-standard vendors like Basler, Baumer, Allied Vision, FLIR, and others.
DeepInspect has successfully inspected over 1000 unique SKUs across automotive, pharma, electronics, and FMCG industries. Check out our [case studies](#) to learn more.