Enhancing PCB Quality and Efficiency with DeepInspect®
AI-Powered PCB Inspection: Enhancing Quality and Efficiency with DeepInspect®
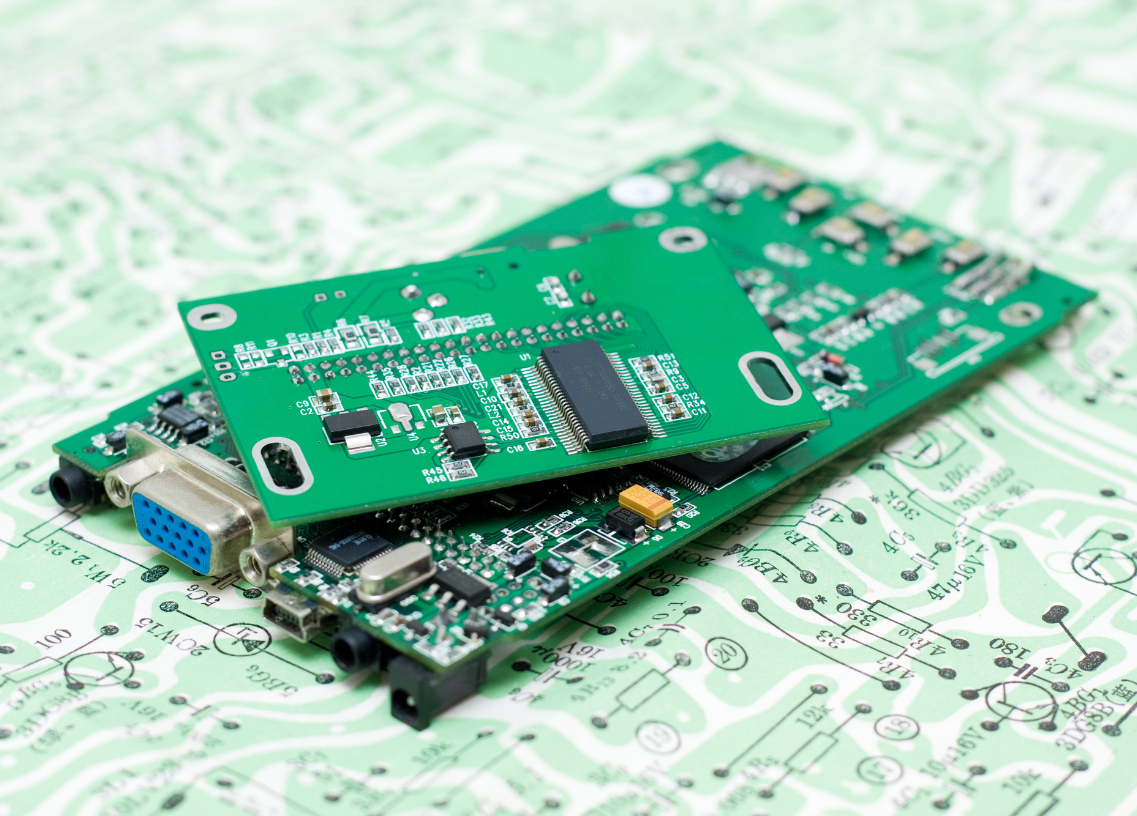
Related Articles
Introduction
Printed Circuit Boards (PCBs) are the foundation of modern electronic devices, enabling seamless electrical connections across multiple components. With increasing complexity in PCB designs, ensuring defect-free manufacturing is more critical than ever. Even minor defects, such as soldering issues, misaligned components, or broken traces, can compromise functionality, reduce product lifespan, and erode consumer trust.
To address these challenges, PCB manufacturers can leverage DeepInspect®, an AI-powered visual quality inspection software that delivers 99.5% accuracy in real-time defect detection. By ensuring precise and reliable quality control, DeepInspect® helps maintain the highest industry standards in PCB production.
What Causes Defects on PCBs?
PCB defects can arise from multiple factors during the manufacturing process, leading to performance issues, reliability concerns, and increased production costs. Some of the primary causes include:
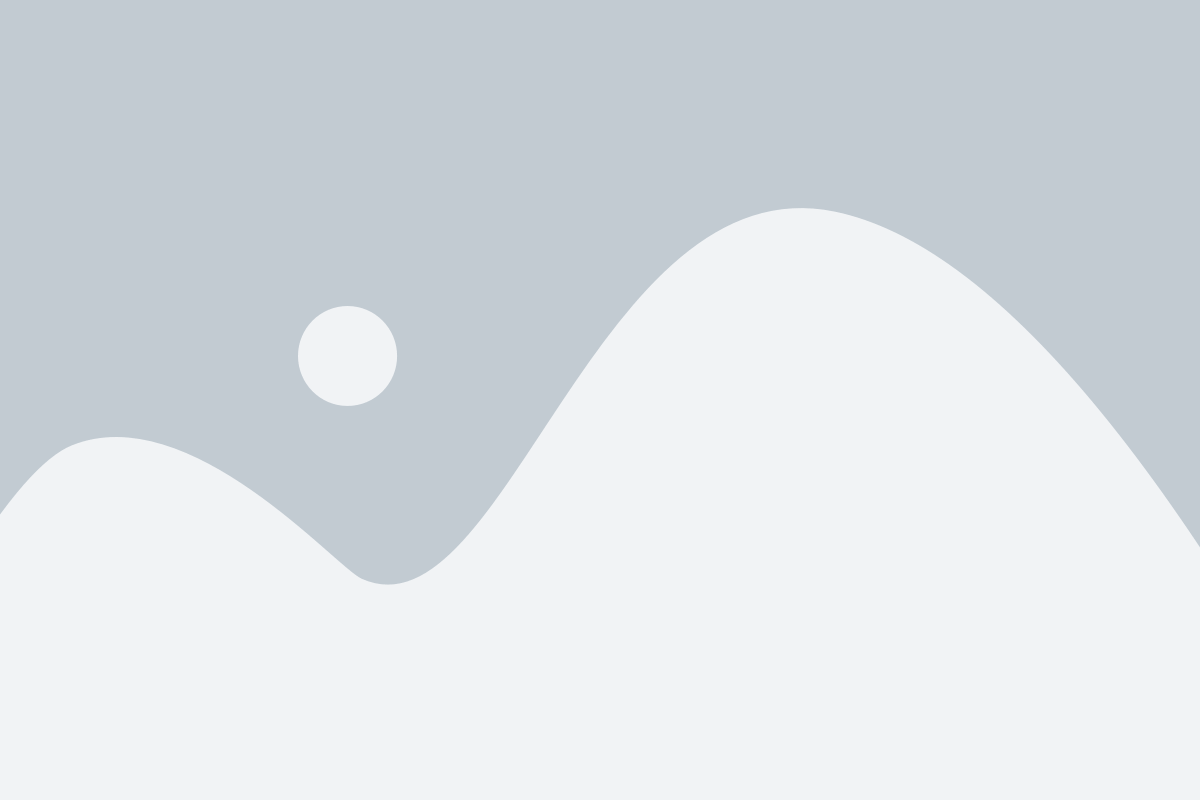
Manufacturing Process Errors
Defects such as soldering issues, misaligned components, etc. often result from improper etching, or inconsistent solder paste application. Even small deviations in these processes can lead to failures
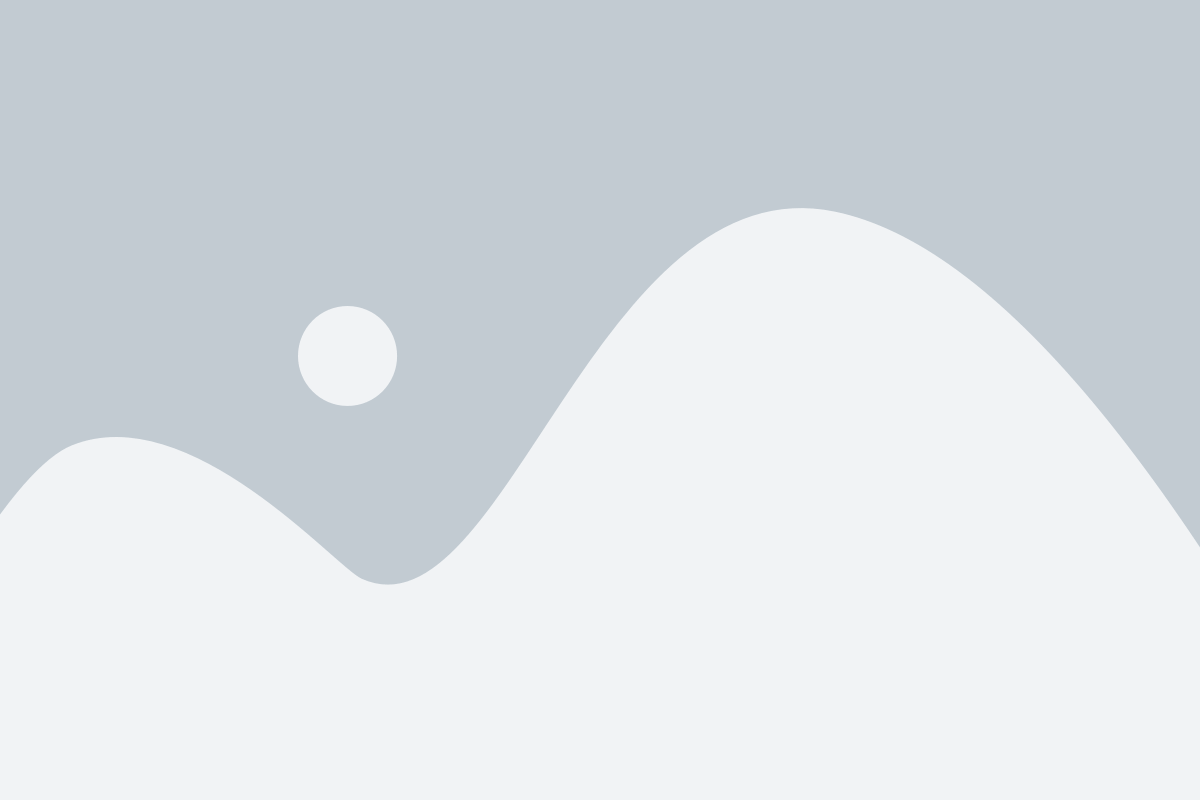
Component Placement Issues
Automated pick-and-place machines operate at high speeds, and any misalignment or incorrect component orientation can cause poor connectivity, electrical malfunctions, complete board
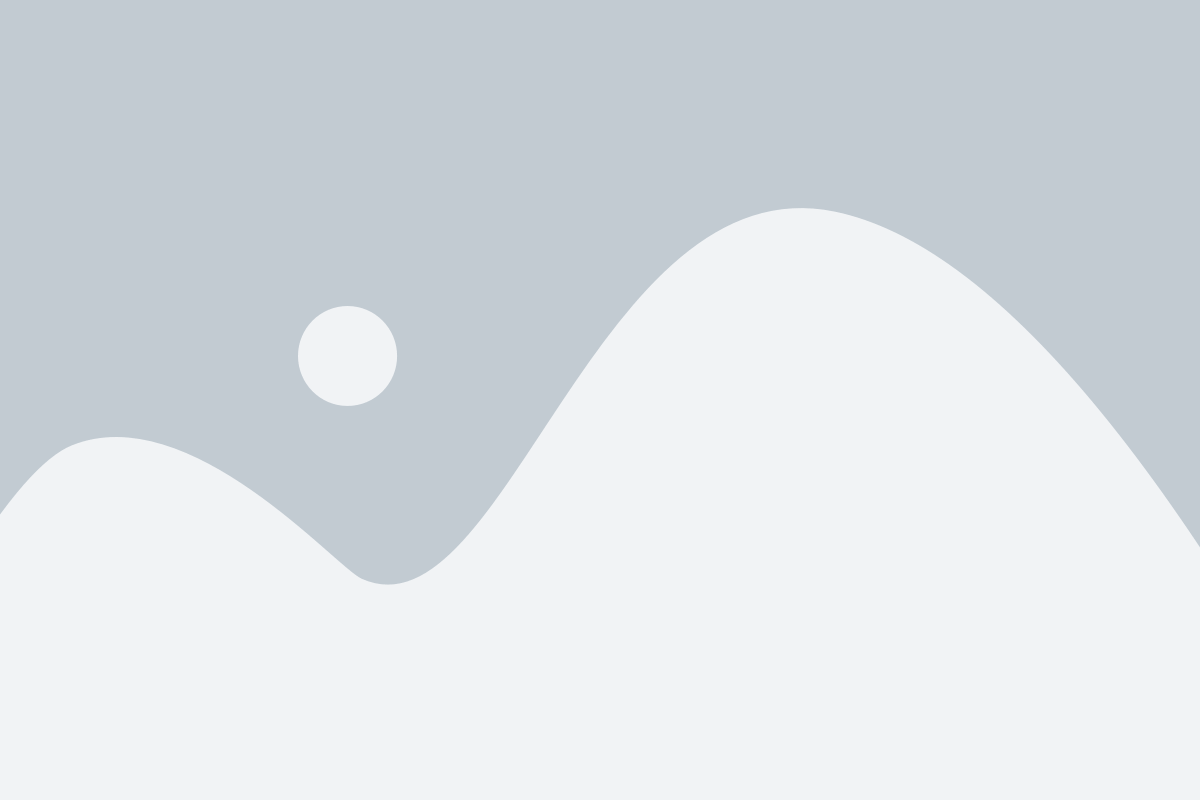
Environmental Contaminants
The presence of dust, metal particles, or debris on a PCB can lead to short circuits, corrosion, or overheating, reducing its lifespan. Cleanroom conditions and proper handling are essential to prevent contamination
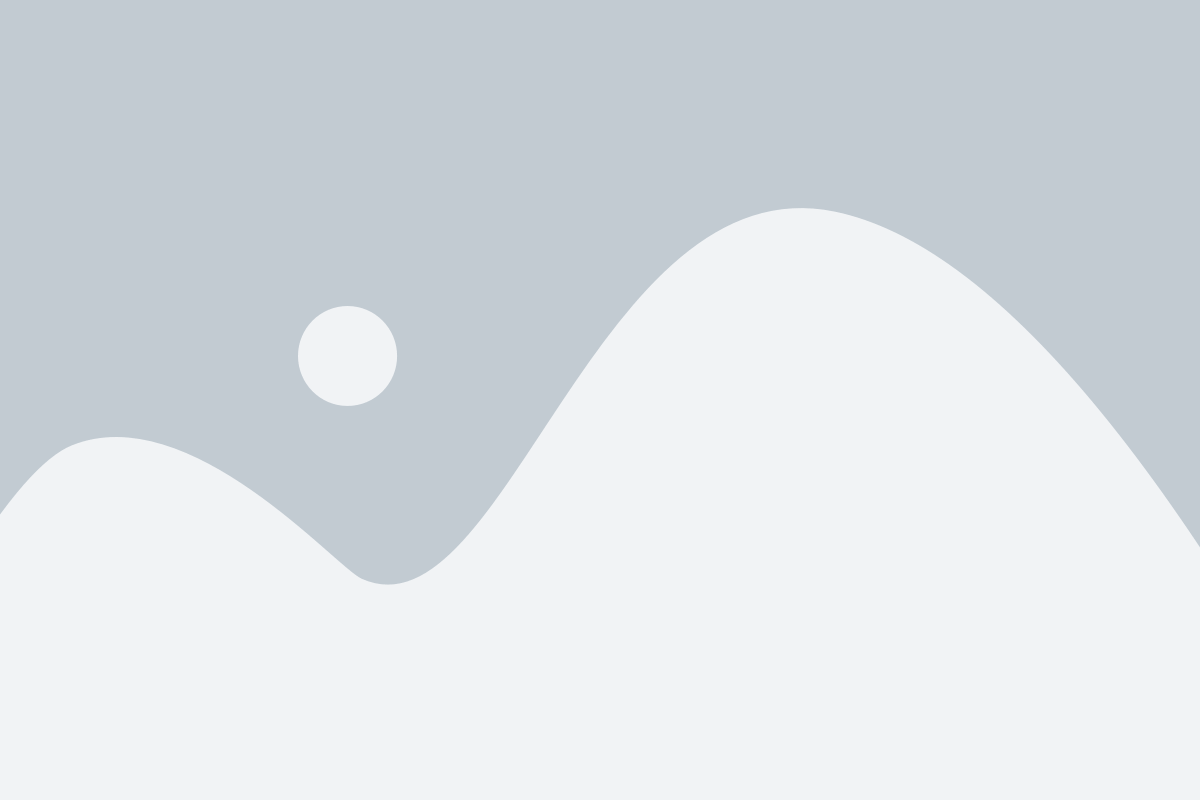
Material Quality and Variability
Using substandard materials, such as low-quality copper layers or weak insulating substrates, can result in delamination, poor conductivity, or increased resistance, impacting overall PCB performance
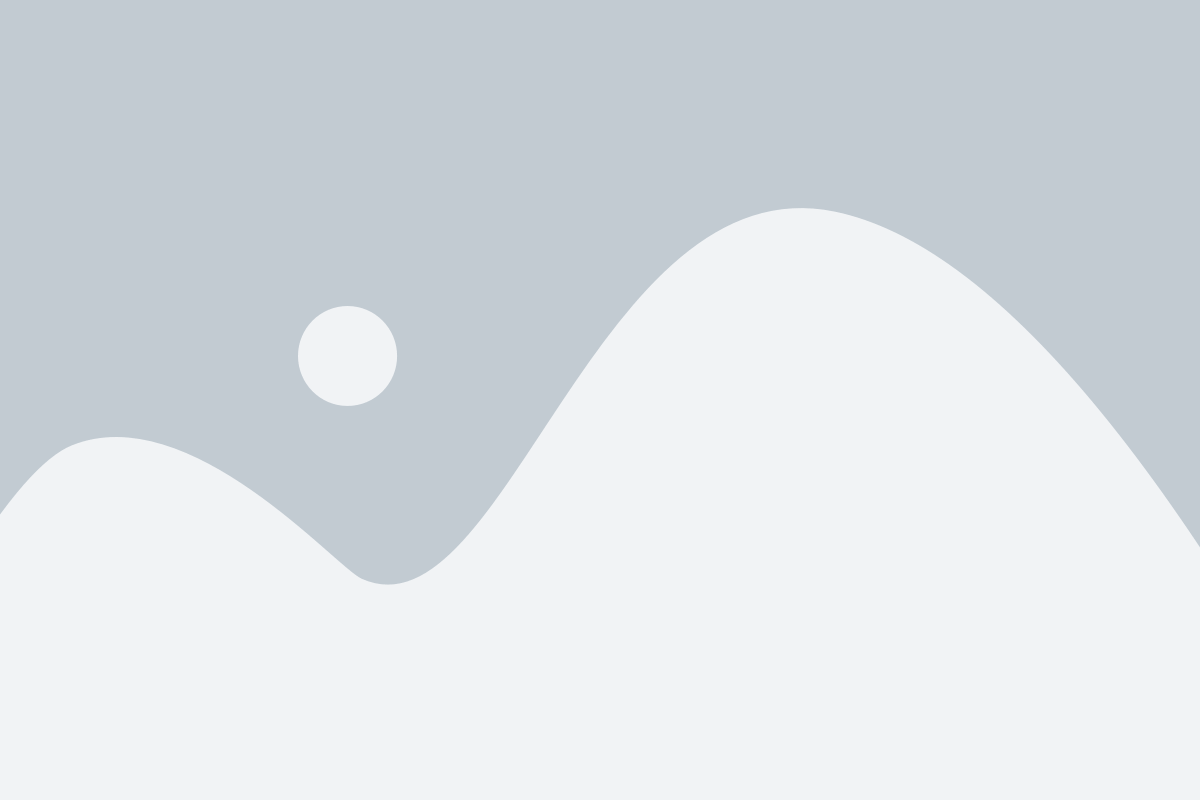
Reflow and Soldering Issues
Uneven heating during the reflow soldering process can cause cold joints, tombstoning, or solder bridging, leading to open circuits or short circuits that affect product reliability
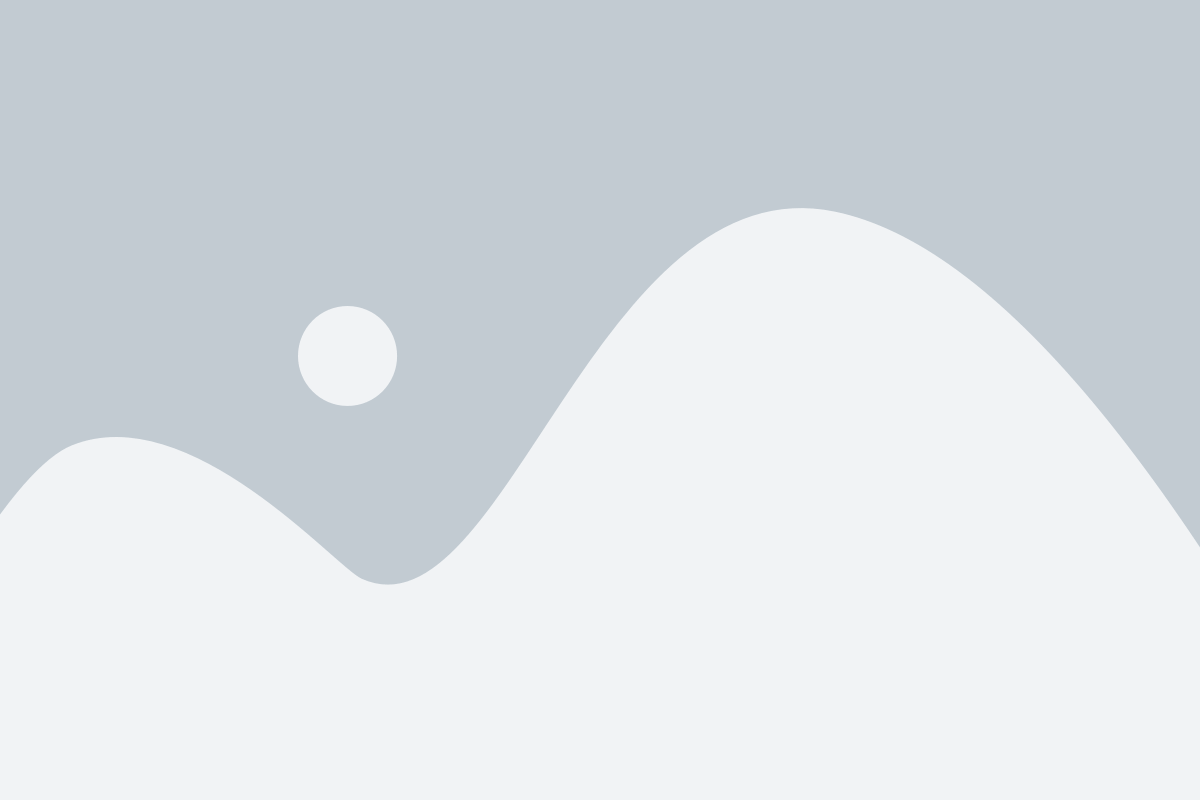
Design Flaws
Errors in PCB layout, trace width, or component spacing can result in electrical noise, signal interference, or power distribution problems, affecting the overall functionality of the board
The Challenges of Defects on PCBs
Defective PCBs pose significant risks to both end consumers and manufacturers, affecting product performance, reliability, and brand reputation. A single faulty PCB can lead to device failures, performance issues, or even safety hazards, especially in industries like automotive, healthcare, and consumer electronics, where precision and reliability are critical. Consumers who experience malfunctioning devices, unexpected breakdowns, or safety concerns due to PCB defects may lose trust in the brand, leading to negative reviews, product returns, and decreased customer loyalty
Higher Production Costs, Increased Scrap Rates, Potential Product Recalls and More..
For manufacturers, these defects result in higher production costs due to rework, increased scrap rates, and potential product recalls. Poor quality control can also lead to regulatory compliance issues, legal liabilities, and financial losses, further damaging a company’s reputation. In a competitive market, maintaining consistent PCB quality is essential for ensuring customer satisfaction, meeting industry standards, and safeguarding brand credibility. Implementing AI-Powered PCB inspection software, DeepInspect® allows manufacturers to eliminate defects early, reduce costs, and maintain a strong market presence.
DeepInspect®: AI-Powered Visual Quality Inspection Software for PCB Manufacturers
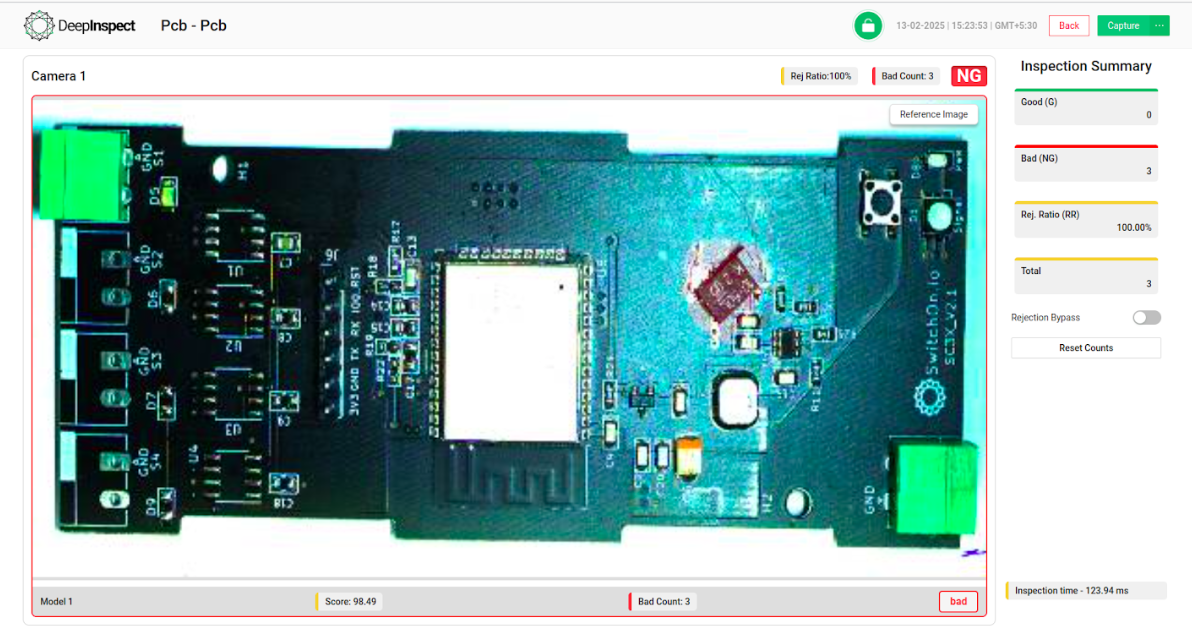
DeepInspect® is an AI-powered visual quality inspection software for PCB manufacturers that help perform multiple inspections on PCBs , including surface defect detection, OCV/OCR, dimension check, object counting, and part presence/absence. The software is designed for efficiency, model training using less than 200 good PCB images and completing the training process in under 45 minutes. With 99.5% accuracy, it effectively identifies critical defects such as soldering issues, misaligned components, broken traces, and foreign particle contamination while maintaining a false positive rate below 0.1%. Once defects are detected, an automated rejection mechanism swiftly removes faulty PCBs from the production line, ensuring seamless manufacturing, reduced waste, and superior product reliability
How Does AI-Powered PCB Inspection Using DeepInspect® Work?
The PCB reaches the DeepInspect® inspection station, where it undergoes high-speed, real-time defect detection to ensure optimal quality. The inspection setup is powered by an Industrial Controller with an i5 processor and GPU, running DeepInspect® software at its core. The system also incorporates Industrial Machine Vision Lights for enhanced visibility and an Industrial Camera for high-resolution imaging, enabling precise defect identification.Once defects are identified, the system automatically activates the rejection mechanism, ensuring that faulty parts do not proceed to the next stage.
The Setup
DeepInspect® Software
Industrial Controller with i5 and GPU
Industrial Machine Vision Lights
Industrial Camera
Mitsubishi IO Module
What Defects in PCBs Can Be Identified Using DeepInspect®?
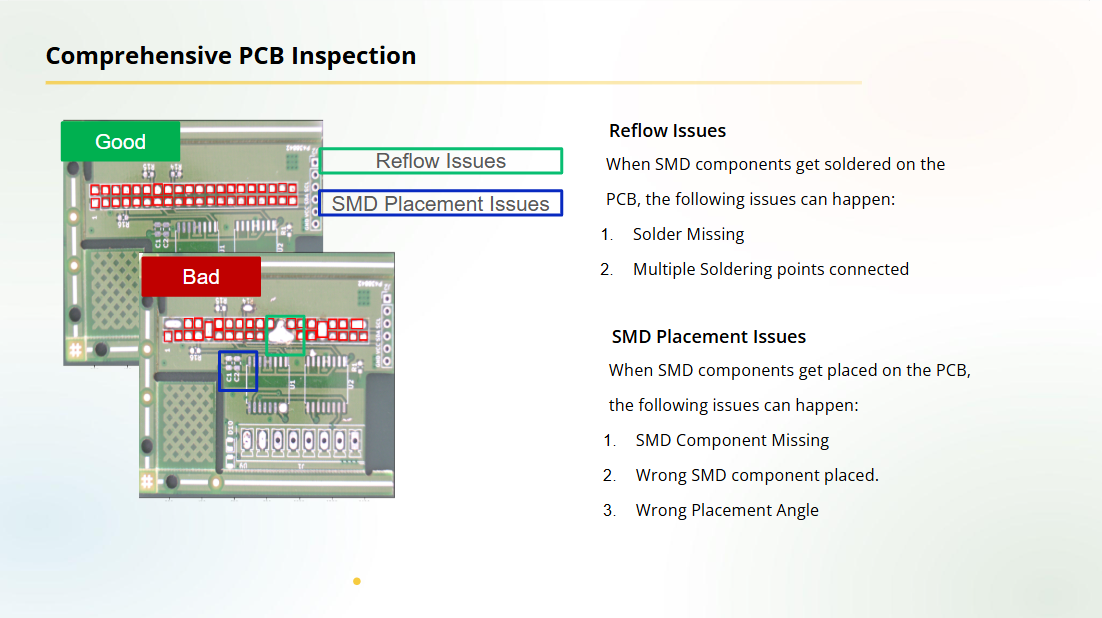
🔹 Soldering Defects – Detects weak or missing solder joints that may cause poor conductivity or circuit failure.
🔹 Reflow Issues – Identifies missing solder and unintended multiple connections that can lead to open circuits or short circuits.
🔹 Misaligned SMD Components – Flags misalignment, missing components, or incorrect placement angles that can impact circuit functionality.
🔹 Foreign Particles – Detects dust, debris, or metal shavings that can cause short circuits, overheating, or reliability issues.
🔹 Broken Traces – Identifies disrupted electrical pathways, preventing potential device malfunctions

Conclusion
In the fast-paced world of PCB manufacturing, maintaining high-quality standards is essential to ensuring product reliability and customer satisfaction. By leveraging DeepInspect®, PCB manufacturers can confidently deliver flawless circuit boards, enhance brand reputation, and achieve long-term success in a rapidly evolving electronics industry. Also, by detecting PCB defects early, DeepInspect® prevents costly rework, enhances product reliability, and ensures compliance with industry quality standards.
Let's Discuss How We Can Transform Your Operations!
FAQ’s :
DeepInspect uses readily available industrial-grade hardware to ensure high repeatability and long lifespan. We provide a basic kit to help you get started, which includes a controller, camera, lights, and a PLC.
DeepInspect supports inspection speeds of up to 1000 parts per minute. The final speed depends on various factors, such as the number of cameras, lighting, and other line conditions. If you have a requirement above 1000 PPM, please contact us.
We support Area Scan, Line Scan, and Thermal cameras. Our software is compatible with industry-standard vendors like Basler, Baumer, Allied Vision, FLIR, and others.
DeepInspect has successfully inspected over 1000 unique SKUs across automotive, pharma, electronics, and FMCG industries. Check out our [case studies](#) to learn more.
Curious to Learn More?
Download the full use case here!